【壓縮機網】引言
隨著某廠規模越來越大,其壓縮空氣站裝機容量已從每分鐘數百立方逼近千立方;按氣質要求可大致分為儀用氣、輸送氣和一般工廠用氣;根據地域和用途不同,目前在用的后處理設備多采用冷凍式、吸附式或冷凍+吸附組合式。近二十年來,空壓機已由活塞式過渡到螺桿式,近年來一些大型空壓站開始采用離心機或離心主供/螺桿調峰組合式。目前,在用各類壓縮機幾乎占用了全國發電量的10%,而與其配套的后處理設備能耗約占空壓機輸入功率的10%~20%,所以空壓系統節能減排日益受到關注。本文主要結合某廠特點介紹目前空壓機及其后處理設備在節能減排方面的一些新動態和新技術,以供設計、采購、運行人員參考。
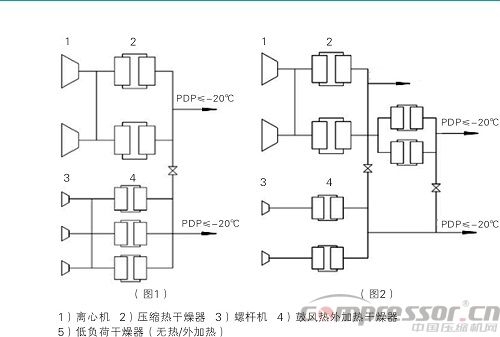
1、2012版壓縮空氣站設計規范有關空壓機選型的條文及影響
1.1原文:新《規范》規定:當單臺壓縮機額定電機功率大于300kW時,不宜選用單級噴油螺桿壓縮機。
編制說明:因為單級噴油螺桿壓縮機機組比功率比活塞壓縮機通常要高10%,比離心壓縮機要高15%,從節能角度考慮,當單臺壓縮機額定電機功率大于300kW(相當于1MPa、60m3/min螺桿壓縮機功率)時,不宜選用。
筆者認為將螺桿與離心機劃線為60m3,主要因為離心機排氣量達60m3時,大多采用三級壓縮,使其更接近等溫壓縮,整機功率亦大幅下降。
1.2離心/螺桿組合工藝流程及說明
圖1采用低露點(≤-20℃)壓縮熱干燥器,與鼓風外加熱的露點相同,兩個系統可互換。圖2壓縮熱干燥器采用傳統型,壓力露點小于等于-3℃,可滿足輸送和一般工廠用氣,部分氣體再串聯較小型的儀表用氣干燥器(低負荷)。螺桿系統通過兩個旁通分別與輸送用氣和一般工廠用氣聯通作為其補充。
2、2012版壓縮空氣站設計規范有關于干燥器選型的條文
2.1原文:“工作壓力小于10MPa、單臺處理氣量大于20m3/min或工作壓力大于等于10MPa、單臺處理氣量大于3m3/min的吸附式干燥裝置,宜采用加熱再生吸附式干燥裝置或壓縮熱再生吸附式干燥裝置”,“壓縮空氣濕度等級要求不低于5級時,應選用冷凍式干燥裝置或壓縮熱再生吸附式干燥裝置”。
編制說明:目前常見的壓縮空氣干燥裝置中,干燥裝置相當于壓縮機耗能的比例,冷凍式約為3~5%,加熱再生吸附式約為8~10%,無熱再生吸附式、微熱再生吸附式約為18%,壓縮熱再生吸附式為1~2%。在一般情況下,為節約能耗,選型干燥裝置時,在滿足干燥要求的前提下應盡可能選用能耗少的干燥裝置。
2.2目前市場上流行的第一代無熱、小微熱(短流程)、大微熱(長流程)吸附式干燥器以及冷干+吸附(第一代無熱、微熱)由于大量消耗高品質產品氣(10%~20%),將逐步退出市場,取而代之的是與螺桿機配套的鼓風外加熱和與離心機配套的壓縮熱(余熱)干燥器以及它們的升級換代產品第三、四代零氣耗、低露點、多功能型。值得注意的是:
1)由于近十年離心機的技術進步、品牌離心機排氣溫度已下行至90~110℃(原為120~150℃),在此溫度下的壓縮熱脫水干燥能力已不能達到其它吸附式干燥器壓力露點-20℃功能,因此該條文將其應用納入冷干機類或介于冷干機與吸附式之間的干燥器產品。
2)干燥器節能減排、降低運行費用的核心技術是不用或少用產品氣,因為產品氣成本構成中電價僅占4成左右,其余6成為固定資產折舊、水、油、汽、管理、人工成本等。
以排氣量為100m3為例,干燥器耗電占壓縮機輸入功率5%(550kW)計,耗氣5%,電價0.70元/kWh,氣耗0.16元/m3計:
則電費:0.70×550kW×5%=19.25元/h,氣費 0.16×100m3×60min×5%=48元/h
在所謂相同“能耗”比例下,電費占產品氣的成本比例為:19.25/48=0.4
按每年運行300天,每天24h計:
氣費比電費多:(48-19.25)×300×24 =20.7 萬元/年
3)壓縮熱干燥器的兩大先天性缺陷,使其不能邁入其它吸附式干燥器低露點行列,除非采用第三、四代改良型。
各種型式無油機不同排氣溫度下再生所能達到的產品氣露點,見表1,大致可歸納為再生氣溫度每提高10℃,產品氣露點可降低2~3℃。
凡有熱再生型必設吹冷程序,一般從塔平均溫度100℃降至50℃,需消耗5%以上產品氣,按加熱/吹冷2/2小時計,吹冷瞬時進氣流量需8%~10%左右,至于樣本上所標注的1%~2%等均不可信。此外中大型干燥器吸附熱導致進排氣溫差達8~13℃,即吹冷氣本身已達50℃左右,即使加大吹冷氣量也無法吹冷至常溫,通常吹冷結束塔內平均溫度仍可達70℃左右。需切換后用較低溫度的進氣帶出熱量,同時排出的產品氣露點和自身溫度亦上升10~20℃,時間約需0.5~1小時,即行業中稱為的“露點漂移”。為了使壓縮熱型干燥器接近零氣耗、低露點和低漂移,行業中用了二十多年時間產生了第三代和第四代機,包括壓縮熱和鼓風外加熱。
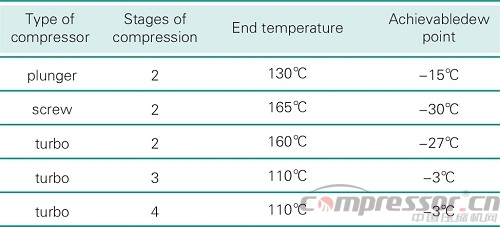
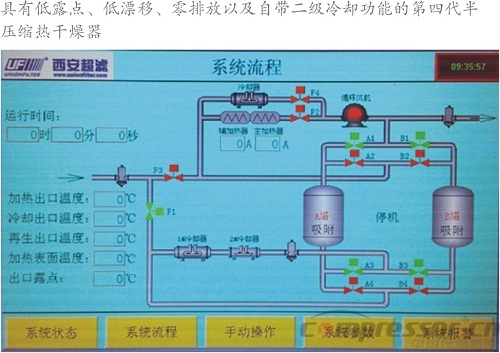
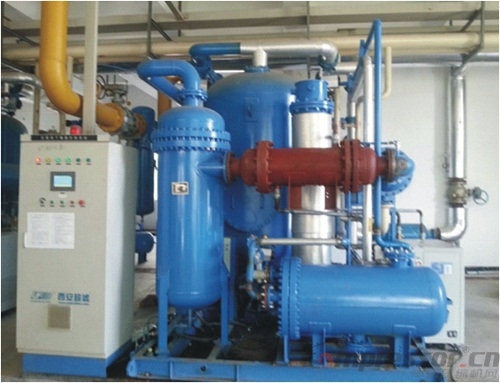
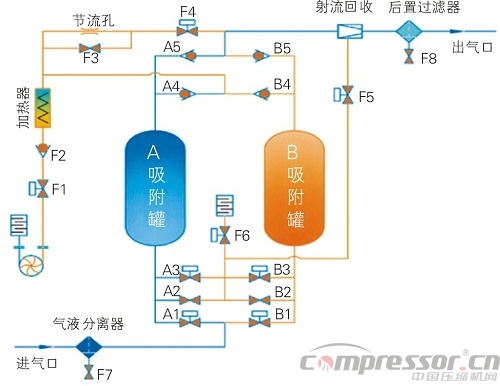
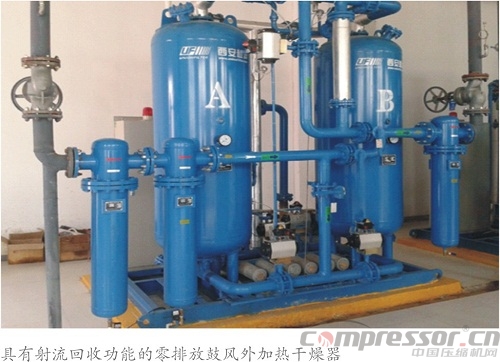
3、對冷凍+吸附的重新定義
冷干加吸附是干燥脫水裝置中的一種特例,但作為一種基本配置大面積推廣則是不可取的。畢竟它以兩倍的占地面積、兩倍的采購成本、兩倍的壓差和幾乎兩倍的運行費用去完成原本可用一臺機完成的功能。真理往前走一步就變成謬論,但它的思路仍可借鑒,即空壓機排氣溫度在常溫時(25~45℃),冷卻除水是z*經濟適用的方法。
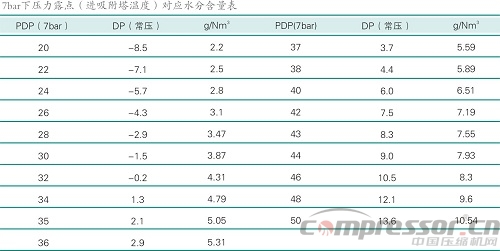
從表中可看出,以30℃為基準,當氣溫增至35℃/38℃/43℃時,壓縮空氣中所攜帶的含水量將增加30%/50%/100%,因此,采用成熟工業冷水機組和水冷卻器,即可在原32℃的工業冷卻水和后冷卻器基礎上再降低氣體溫度5~8℃,即可將氣體中的含水量降低30~50%,此時對吸附式干燥器可做到一箭四雕:
1)降低進氣溫度幾乎可達到同時1:1降低產品氣露點溫度;
2)降低水負荷30~50%,避免吸附塔提前穿透;
3)降下來的水負荷亦同時降低吸附熱,即同時降低了吹冷氣的起點溫度;
4)避免了過多吸附熱導致吸附劑溫度上升,相當于降低了吸附劑有效吸附量(約10~30%),確保了在整個吸附周期吸附劑不被水分穿透。
4、結束語
節能減排是國家大事,是空壓系統設計、采購、運行的重要考量內容,吸附式干燥器應z*大限度的利用系統中的熱源和環境中的冷量,大膽采用新工藝、新結構、新技術、加速推進空壓機站節能減排進程、利國、利民、利己。目前在用和正在設計選型中的吸附式干燥器、高能耗的一代機占95%以上,節能減排源頭是設計選型,升級換代主體是制造商,客戶是直接受益者,供貨方不應利用消費者的幼稚和專業知識的缺乏去愚弄客戶,而應培養促進消費者的成熟。限制無熱,淘汰微熱,發展有熱,推廣余熱。
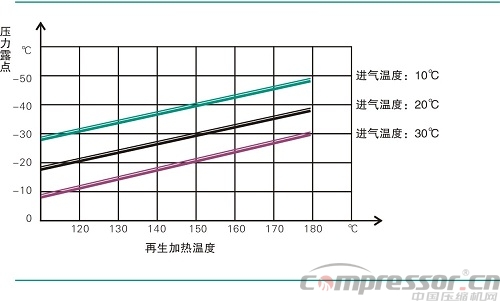
節能減排從我做起,從手下項目起步。三方協力爭取5~10年不僅制造規模接近國際同行,技術性能和節能減排技術也要達到國際水平。
【壓縮機網】引言
隨著某廠規模越來越大,其壓縮空氣站裝機容量已從每分鐘數百立方逼近千立方;按氣質要求可大致分為儀用氣、輸送氣和一般工廠用氣;根據地域和用途不同,目前在用的后處理設備多采用冷凍式、吸附式或冷凍+吸附組合式。近二十年來,空壓機已由活塞式過渡到螺桿式,近年來一些大型空壓站開始采用離心機或離心主供/螺桿調峰組合式。目前,在用各類壓縮機幾乎占用了全國發電量的10%,而與其配套的后處理設備能耗約占空壓機輸入功率的10%~20%,所以空壓系統節能減排日益受到關注。本文主要結合某廠特點介紹目前空壓機及其后處理設備在節能減排方面的一些新動態和新技術,以供設計、采購、運行人員參考。
1、2012版壓縮空氣站設計規范有關空壓機選型的條文及影響
1.1原文:新《規范》規定:當單臺壓縮機額定電機功率大于300kW時,不宜選用單級噴油螺桿壓縮機。
編制說明:因為單級噴油螺桿壓縮機機組比功率比活塞壓縮機通常要高10%,比離心壓縮機要高15%,從節能角度考慮,當單臺壓縮機額定電機功率大于300kW(相當于1MPa、60m3/min螺桿壓縮機功率)時,不宜選用。
筆者認為將螺桿與離心機劃線為60m3,主要因為離心機排氣量達60m3時,大多采用三級壓縮,使其更接近等溫壓縮,整機功率亦大幅下降。
1.2離心/螺桿組合工藝流程及說明
圖1采用低露點(≤-20℃)壓縮熱干燥器,與鼓風外加熱的露點相同,兩個系統可互換。圖2壓縮熱干燥器采用傳統型,壓力露點小于等于-3℃,可滿足輸送和一般工廠用氣,部分氣體再串聯較小型的儀表用氣干燥器(低負荷)。螺桿系統通過兩個旁通分別與輸送用氣和一般工廠用氣聯通作為其補充。
2、2012版壓縮空氣站設計規范有關于干燥器選型的條文
2.1原文:“工作壓力小于10MPa、單臺處理氣量大于20m3/min或工作壓力大于等于10MPa、單臺處理氣量大于3m3/min的吸附式干燥裝置,宜采用加熱再生吸附式干燥裝置或壓縮熱再生吸附式干燥裝置”,“壓縮空氣濕度等級要求不低于5級時,應選用冷凍式干燥裝置或壓縮熱再生吸附式干燥裝置”。
編制說明:目前常見的壓縮空氣干燥裝置中,干燥裝置相當于壓縮機耗能的比例,冷凍式約為3~5%,加熱再生吸附式約為8~10%,無熱再生吸附式、微熱再生吸附式約為18%,壓縮熱再生吸附式為1~2%。在一般情況下,為節約能耗,選型干燥裝置時,在滿足干燥要求的前提下應盡可能選用能耗少的干燥裝置。
2.2目前市場上流行的第一代無熱、小微熱(短流程)、大微熱(長流程)吸附式干燥器以及冷干+吸附(第一代無熱、微熱)由于大量消耗高品質產品氣(10%~20%),將逐步退出市場,取而代之的是與螺桿機配套的鼓風外加熱和與離心機配套的壓縮熱(余熱)干燥器以及它們的升級換代產品第三、四代零氣耗、低露點、多功能型。值得注意的是:
1)由于近十年離心機的技術進步、品牌離心機排氣溫度已下行至90~110℃(原為120~150℃),在此溫度下的壓縮熱脫水干燥能力已不能達到其它吸附式干燥器壓力露點-20℃功能,因此該條文將其應用納入冷干機類或介于冷干機與吸附式之間的干燥器產品。
2)干燥器節能減排、降低運行費用的核心技術是不用或少用產品氣,因為產品氣成本構成中電價僅占4成左右,其余6成為固定資產折舊、水、油、汽、管理、人工成本等。
以排氣量為100m3為例,干燥器耗電占壓縮機輸入功率5%(550kW)計,耗氣5%,電價0.70元/kWh,氣耗0.16元/m3計:
則電費:0.70×550kW×5%=19.25元/h,氣費 0.16×100m3×60min×5%=48元/h
在所謂相同“能耗”比例下,電費占產品氣的成本比例為:19.25/48=0.4
按每年運行300天,每天24h計:
氣費比電費多:(48-19.25)×300×24 =20.7 萬元/年
3)壓縮熱干燥器的兩大先天性缺陷,使其不能邁入其它吸附式干燥器低露點行列,除非采用第三、四代改良型。
各種型式無油機不同排氣溫度下再生所能達到的產品氣露點,見表1,大致可歸納為再生氣溫度每提高10℃,產品氣露點可降低2~3℃。
凡有熱再生型必設吹冷程序,一般從塔平均溫度100℃降至50℃,需消耗5%以上產品氣,按加熱/吹冷2/2小時計,吹冷瞬時進氣流量需8%~10%左右,至于樣本上所標注的1%~2%等均不可信。此外中大型干燥器吸附熱導致進排氣溫差達8~13℃,即吹冷氣本身已達50℃左右,即使加大吹冷氣量也無法吹冷至常溫,通常吹冷結束塔內平均溫度仍可達70℃左右。需切換后用較低溫度的進氣帶出熱量,同時排出的產品氣露點和自身溫度亦上升10~20℃,時間約需0.5~1小時,即行業中稱為的“露點漂移”。為了使壓縮熱型干燥器接近零氣耗、低露點和低漂移,行業中用了二十多年時間產生了第三代和第四代機,包括壓縮熱和鼓風外加熱。
3、對冷凍+吸附的重新定義
冷干加吸附是干燥脫水裝置中的一種特例,但作為一種基本配置大面積推廣則是不可取的。畢竟它以兩倍的占地面積、兩倍的采購成本、兩倍的壓差和幾乎兩倍的運行費用去完成原本可用一臺機完成的功能。真理往前走一步就變成謬論,但它的思路仍可借鑒,即空壓機排氣溫度在常溫時(25~45℃),冷卻除水是z*經濟適用的方法。
從表中可看出,以30℃為基準,當氣溫增至35℃/38℃/43℃時,壓縮空氣中所攜帶的含水量將增加30%/50%/100%,因此,采用成熟工業冷水機組和水冷卻器,即可在原32℃的工業冷卻水和后冷卻器基礎上再降低氣體溫度5~8℃,即可將氣體中的含水量降低30~50%,此時對吸附式干燥器可做到一箭四雕:
1)降低進氣溫度幾乎可達到同時1:1降低產品氣露點溫度;
2)降低水負荷30~50%,避免吸附塔提前穿透;
3)降下來的水負荷亦同時降低吸附熱,即同時降低了吹冷氣的起點溫度;
4)避免了過多吸附熱導致吸附劑溫度上升,相當于降低了吸附劑有效吸附量(約10~30%),確保了在整個吸附周期吸附劑不被水分穿透。
4、結束語
節能減排是國家大事,是空壓系統設計、采購、運行的重要考量內容,吸附式干燥器應z*大限度的利用系統中的熱源和環境中的冷量,大膽采用新工藝、新結構、新技術、加速推進空壓機站節能減排進程、利國、利民、利己。目前在用和正在設計選型中的吸附式干燥器、高能耗的一代機占95%以上,節能減排源頭是設計選型,升級換代主體是制造商,客戶是直接受益者,供貨方不應利用消費者的幼稚和專業知識的缺乏去愚弄客戶,而應培養促進消費者的成熟。限制無熱,淘汰微熱,發展有熱,推廣余熱。
節能減排從我做起,從手下項目起步。三方協力爭取5~10年不僅制造規模接近國際同行,技術性能和節能減排技術也要達到國際水平。
網友評論
條評論
最新評論